TIN MINING AREA
The two (2) parcels of Mining Lease (ML) are located adjoining to each other, ML 1/2020 PT 5571 and ML 2/2020 PT 822. The leased land of ML 2/2020 lies directly to the north of ML 1/2020, and is situated on two Mukim, namely, Mukim Batang Berjuntai and Mukim Ulu Tinggi.
The mine site is a flat to undulating terrain consisting of bush and overgrowth of weeds and trees left in the wild after tin dredging by previous dredges operated by MMC Corp.
Based on the production record, the average rate of excavation is about 500,000m3 per month, as the mining is now concentrated on the lower depth part of the mining process. Hence, the expected life operation is assessed to be about 15 years. By extrapolation, as the potential composite ore reserve can be estimated to be approximately 9,249.17 tonne.
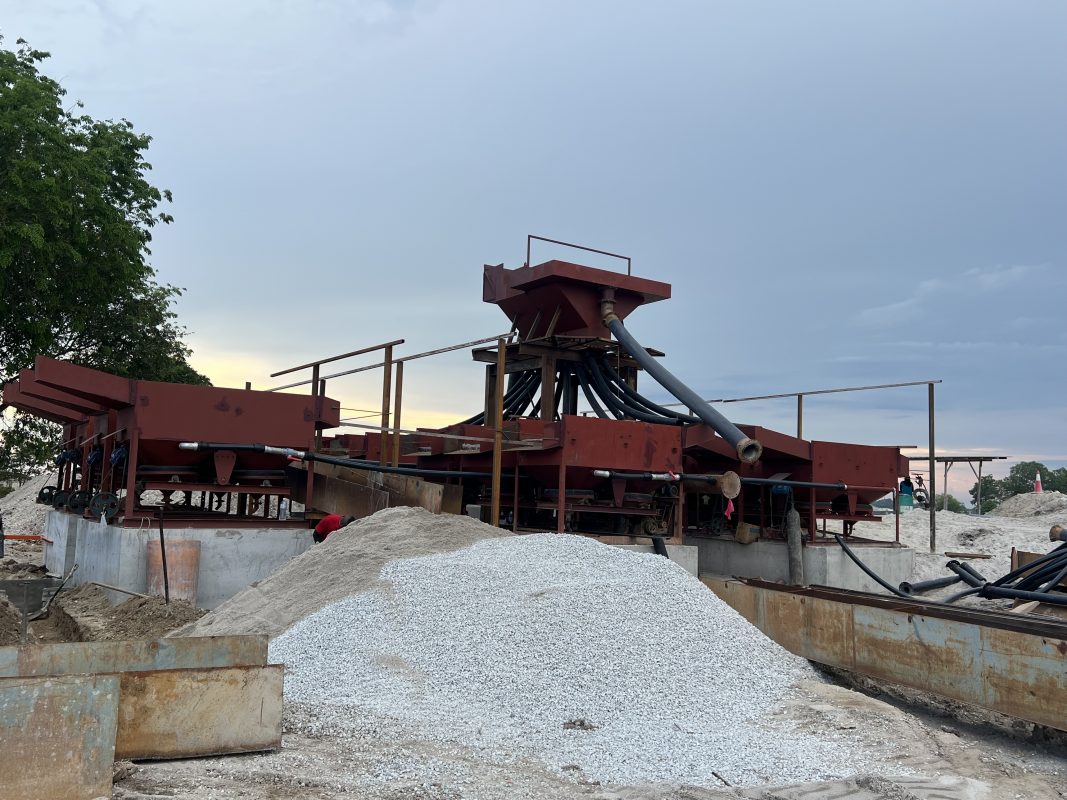
METHOD OF TIN ORE EXTRACTION
There are two (2) method of tin ore extraction that KL Larut use in this mining operation:
- Dry Opencast Method with Palong;
- Dredge Method with Jig.
Dry Opencast mining method involves direct excavation of tin bearing materials to expose the bottom layer of tin deposits.
The first stage starts with removal of surface vegetation, and then the unwanted overburden materials will be excavated and removed by using hydraulic excavators in order to reach the sandy and tin ore layers.
Those vegetation and overburden materials so removed will be transported by tipper lorries to be dumped at the designated dry dump area of the project site. Raw ore material will be excavated by hydraulic excavator and transported to the palong processing plant that consists of a screen. For wet discharge tailing retention ponds are located near to the palong.
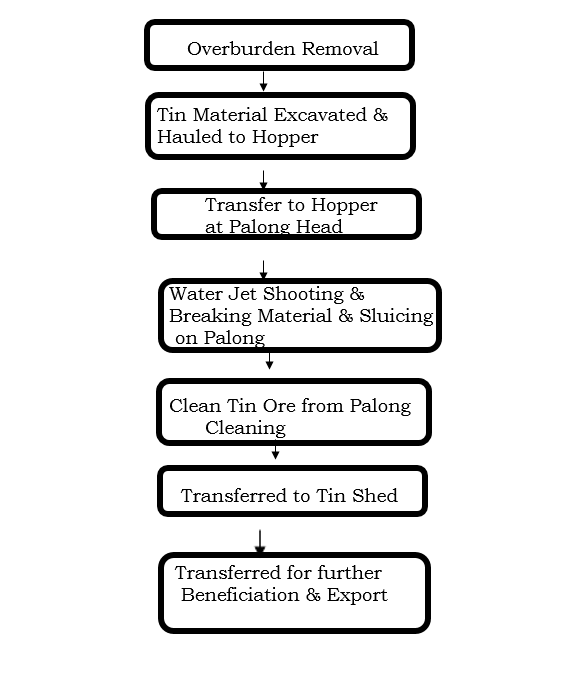
Project Site Photos
DREDGE METHOD WITH JIG
The dredges will float on the surface of the water in the mining pond. This takes away the need to dewater the pond over which tin mining is to be conducted.
The larger dredge will be able to reach a depth of 35 – 40 m below the water level, whilst the smaller dredge will be able to dredge down to 40 feet below.
The tin mining will be using powerful Cutter suction of a vertical gravel pump to be installed on board the pontoon anchored to the banks of the pond by cables on all sides. The anchors have to be properly secured to the ground on the shores, with proper piling deep enough to ensure the anchors will not give way and causing serious damage to property and workers and people nearby.
The minerals sucked by the suction pump or by the vertical placed on the pontoon will be pumped simultaneously to the hopper of the sieving hooper and tank, big enough to cater to the volume of water and sandy materials. The hopper and tank will consist of sieve whereby the water and sand will flow out through the sieve while the larger boulders and solid materials will be rejected. The water and tin ore bearing materials will then flow over the palong till the end, whereby, the heavier tin ores will sink to the bottom, while the sand overflows the palong to the tailing sump at the end.
PROCESSING AND RECOVERY BY JIGS
There are six (6) sets of jigs at the project site located at west side of the ML.2/2015. At the cutting depth of 22 m (65 ft.), all the materials from the suction dredges will be pumped to the jigging plant directly for the tin ore recovery. No material from the dredging at that depth will be pumped to the sand processing screen and sluice launder any more. The operation at this stage will be concentrated fully on tin ore mining and recovery.
The grade of tin ore recovered from the jigs is expected to be approximately 50% SnO2 (cassiterite, the main ore of tin) upwards. Those grades of tin ore that fall below 50% will be redressed using manual dressing (“lanchute”) launder / sluice launder constructed on the ground level, built at the tin-shed nearby.
Cleaned tin ore will be dried using vertical column perforated drier heated from the central core. It is a slow drying process with the heat generated using fuel oil.
The dried tin ore will then be removed and shifted to the strong room for storage until sufficient amount is accumulated to be sold to the tin smelter (MSC) for smelting into tin ingots.
FLOWCHART FOR SUCTION CUTTER DREDGES METHOD WITH JIGS
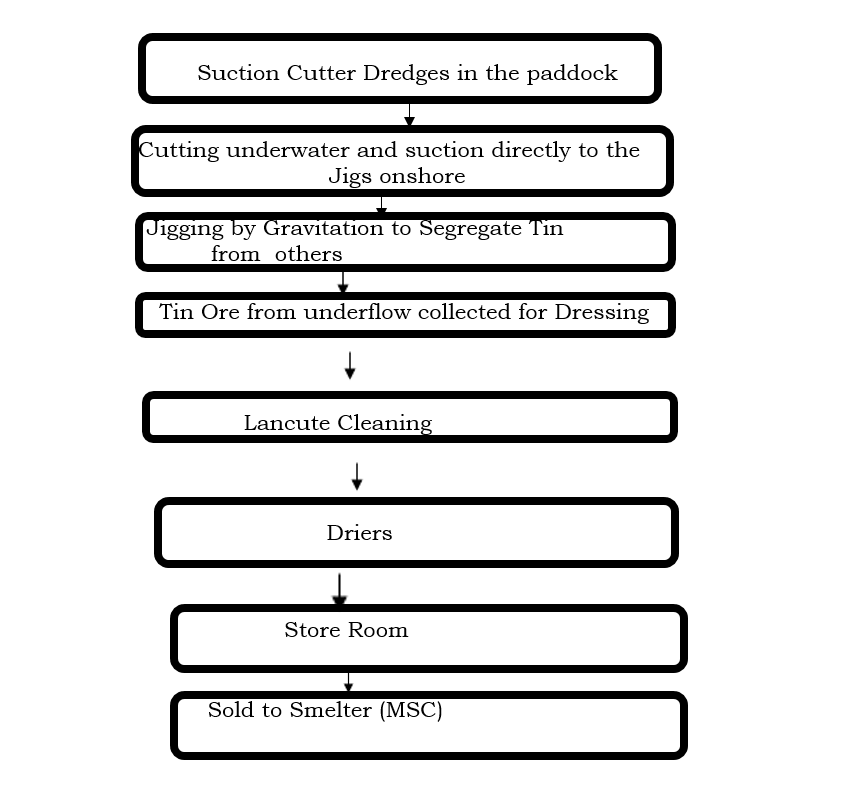